This is a post by NTUC Assistant Secretary-General Melvin Yong. Any extracts should be attributed back to the author, 28 August 2019.
One million MKBF – what is MKBF?
Nope, it is not a swear word. MKBF is an abbreviation that represents the hard work of our rail workers – one that measures rail reliability, by looking at the distance our trains can clock between failures. MBKF refers to Mean Kilometre Between Failures.
Today, Singapore’s MRT system is finally within reach of one million MKBF, the rail reliability target that has been the daily driving force for our rail workers.
Looking back, we have come a long way indeed.
In 2015, our trains were clocking an average of 133,000 MKBF and Singapore’s rail network experienced an average of 2.5 disruptions per month from January to June. By 2017, we have improved it to 181,000 MKBF. This means lesser disruptions!
Fast forward to August 2019, rail reliability has improved exponentially. Today, our rail network has achieved an average of over 950,000 MKBF! Our MRT is now on par with other world-class rail networks globally.
Only 3 Hours Nightly to Carry Out Maintenance Work
Such an achievement would not have been possible without the hard work of our rail workers, who have been working tirelessly to deliver a safe and reliable public transport system for commuters.
Major asset renewal works, such as the replacement of wooden rail sleepers, power rail, and the signaling system, had to be done through the wee hours of the night to ensure that commuters were able to rely on train services in the day. This meant our rail workers had only about 3 hours every night to carry out both routine maintenance as well as the structural improvement works! The early closures and late openings of selected MRT stations helped, providing more engineering hours for our rail workers to carry out and complete their work.
Commuters also have noticed the improvements in rail reliability, with commuter satisfaction in MRT services achieving a new high in 2018, according to the PTC’s Public Transport Customer Satisfaction Survey.
Rail Network to Get More Complex and More Interconnected
With trains as the backbone of our public transport system, reaching one million MKBF is not the end of our journey, but rather, only the beginning.
Our Government has this vision – for all travels to the nearest town centre to be within 20 minutes, and for 9 in 10 peak-period inter-town travels to take 45 minutes or less. To achieve this vision of “20-minute towns and 45-minute city” by 2040, we are expanding our rail network.
Work has already begun. With the inclusion of the Thomson-East Coast Line by 2024, and the new Cross Island Line by 2030, Singapore’s 180km-long rail network will double to 360km. LTA is also studying the feasibility of a new rail line to serve the developing north and northwestern regions, which could benefit more than 400,000 households when completed.
To sustain rail reliability, we need to collectively make three key investments.
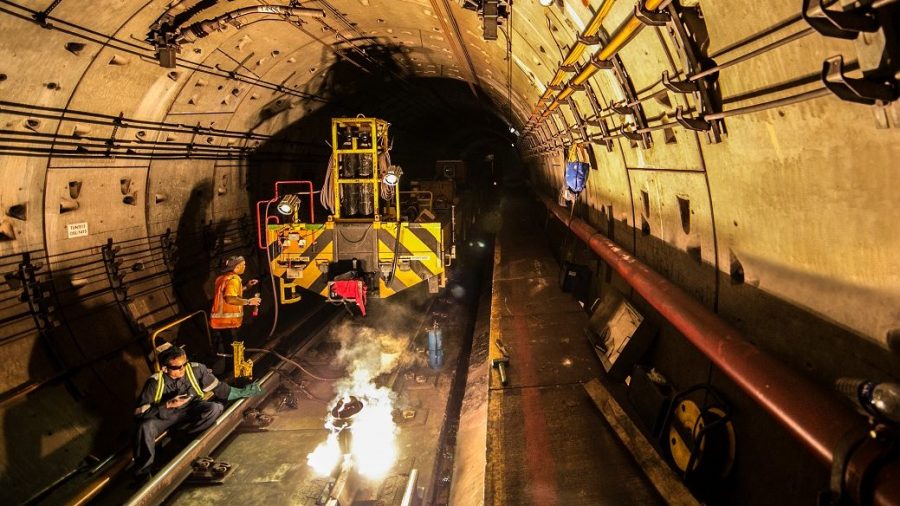
Investment 1: Hire More Rail Workers
Expanding the length of our rail network cannot come at the expense of rail reliability. To ensure that we maintain high levels of rail reliability, we need to increase the strength of our rail workforce as we increase the length of the rail network to ensure sufficient workers to carry out regular maintenance and rail upgrading works.
Today, across our five rail lines, the operators deploy more than 4,000 staff (more than 50 per cent of their headcount) to engineering and maintenance. With the expanding rail network resulting in more interconnectivity and the introduction of new and complex systems, the current rail workforce is too lean to meet the challenges of tomorrow.
But asking the rail operators to hire more workers is a big challenge, as they have made hefty losses in their efforts to improve rail reliability. According to the Transport Ministry, the total cost of running the rail network increased by around $270 million between 2016 and 2017. As fares paid by commuters do not cover operating costs, the rail companies are operating at a loss. In the latest reported financial year, SMRT Trains incurred a loss of $86 million, while SBS Transit’s train division also lost tens of millions of dollars.
Such hefty losses are at odds with the objectives of the New Rail Financing Framework (NRFF). Implemented in 2011, the NRFF sought to create a financially sustainable rail system to allow rail operators to focus on the operations and maintenance of the rail network. Rail operators cannot continue to operate at a loss, else we run the risk of undoing all the good work we have done so far. Can the government review the NRFF to ensure that the rail operators are better financially incentivised for maintaining and running a safe, efficient and reliable rail network?
Investment 2: Training Our Rail Workers
Simply hiring more staff to shore up our lean rail workforce cannot be the only solution. We need to invest in training our workers and have a comprehensive rail manpower development plan, to ensure that they are well-equipped for the technologies of tomorrow.
To do their jobs better, the operators must ensure that they cross-train and deep-skill the rail workforce, so that they can handle the increasing use of digitalisation and automation in the workplace.
In this regard, SMRT has done a good first step by working with the National Transport Workers’ Union (NTWU) to roll out a customised SkillsFuture for Digital Workplace programme for SMRT employees. This programme was rolled out as an initiative by the NTWU-SMRT Company Training Committee (CTC). With the establishment of the CTCs in both SMRT and SBST, the Labour Movement is able to help our operators identify training needs and develop relevant training programmes for workers. Likewise, SBST has worked closely with NTWU since they formed the CTC in end-2018 to upskill and reskill its employees. It has also embarked on its digital journey through training its employees in data and statistical analytics, internet of things application, Robotics and automation application etc.
In addition to rolling out training programmes, the rail industry also needs to recognise and promote technicians with many years of experience but may not have formal paper qualifications. Through my ground visits, I have interacted with many skilled technicians who are very good at what they do, but are unable to progress up the career ladder simply because they do not have a degree. A degree should not be a limiting step towards progression. The industry needs to recognise these veterans as invaluable specialists. Establishing a specialist rail technologist track will certainly go a long way to recognise and provide a career pathway for skilled technicians.
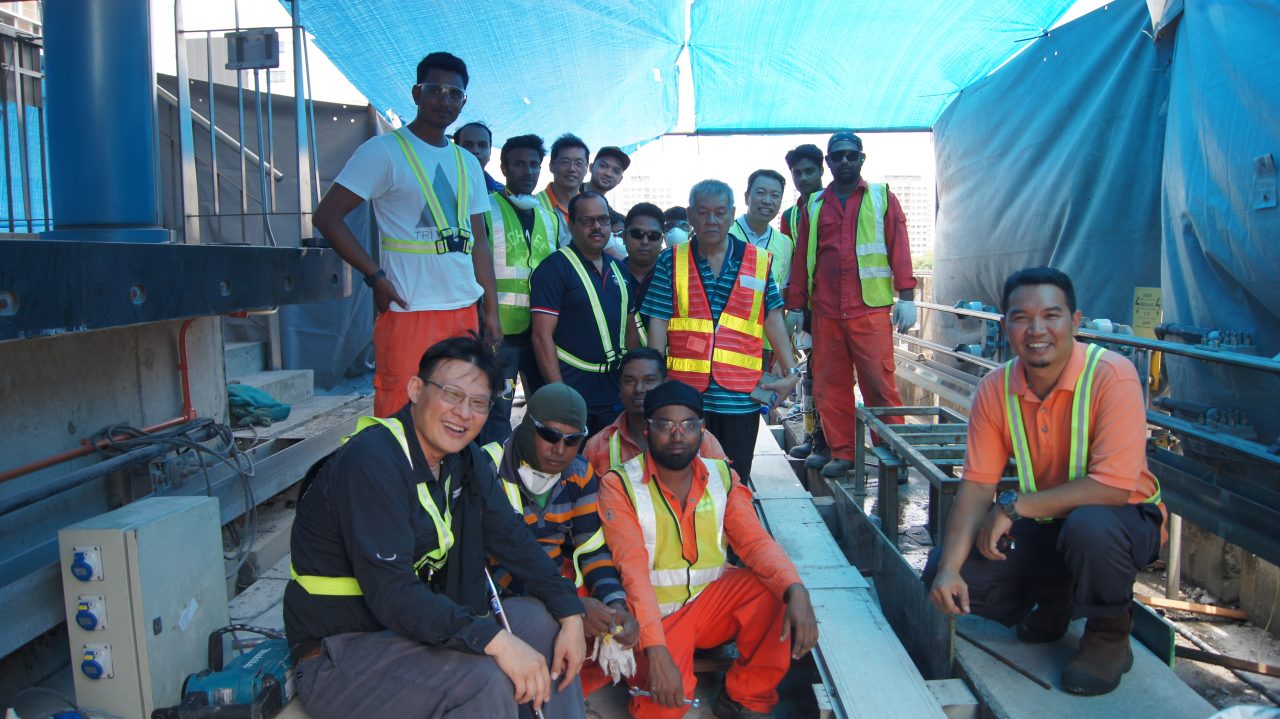
Investment 3: Attracting Young Talents into the Rail Sector
To ensure that our rail industry continues to innovate well into the future, we need to invest now in attracting bright young talents into the sector. Young engineers have told me that the complexities and challenges involved in the rail industry is deeply exciting. With the right progression pathway, I hope many would consider a meaningful career in the sector.
In this regard, NTWU will be working with our partners to set up a chapter for transport engineers – one that can focus on the needs and career development of our transport engineers and technicians.
I call on our tripartite partners to join hands with NTWU. Let us work together to provide a clear progression pathway to attract the best young engineers into the industry.
Conclusion
One million MKBF.
Our rail workers are working hard every day. Asset renewal works continue every night, competing for space and time with routine maintenance work.
We will get to one million MKBF. The challenge is to sustain it when we get there. Therefore, I urge – invest now in our rail workforce.