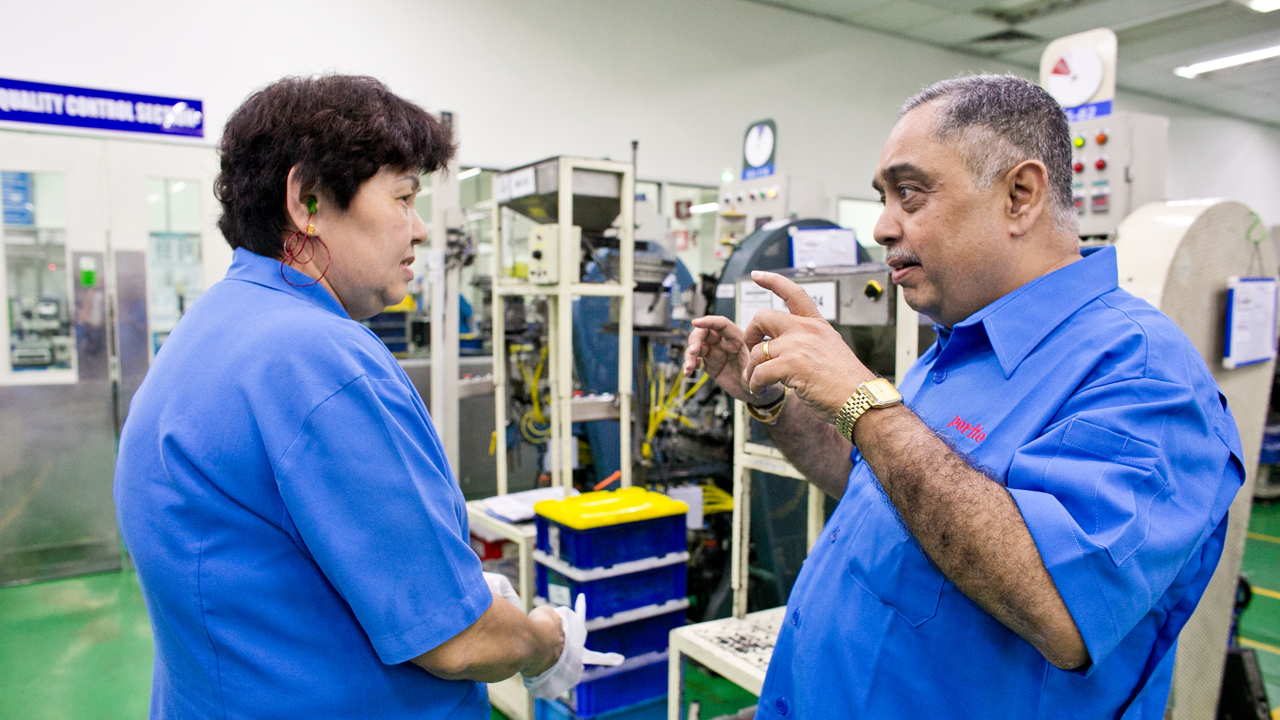
Having joined the ranks of mature workers four years ago, I wanted to find out how companies have been responding to the Labour Movement’s call for job-redesign to keep mature workers employable. I checked out one company which has done just that.
Porite Singapore (Pte) Ltd, whose workers are with the Metal Industries Workers’ Union (MIWU), manufactures metal ball bearings for a range of household electronic products, from your DVD players to washing machines.
On The Job
My job today was to take on the responsibility of an operator at the company’s sizing department where ball bearings are poured into a machine, which then sizes them according to the type of products they are for .
Guiding me was 62-year-old Madam Ong Lai Chew, my mentor for the day.
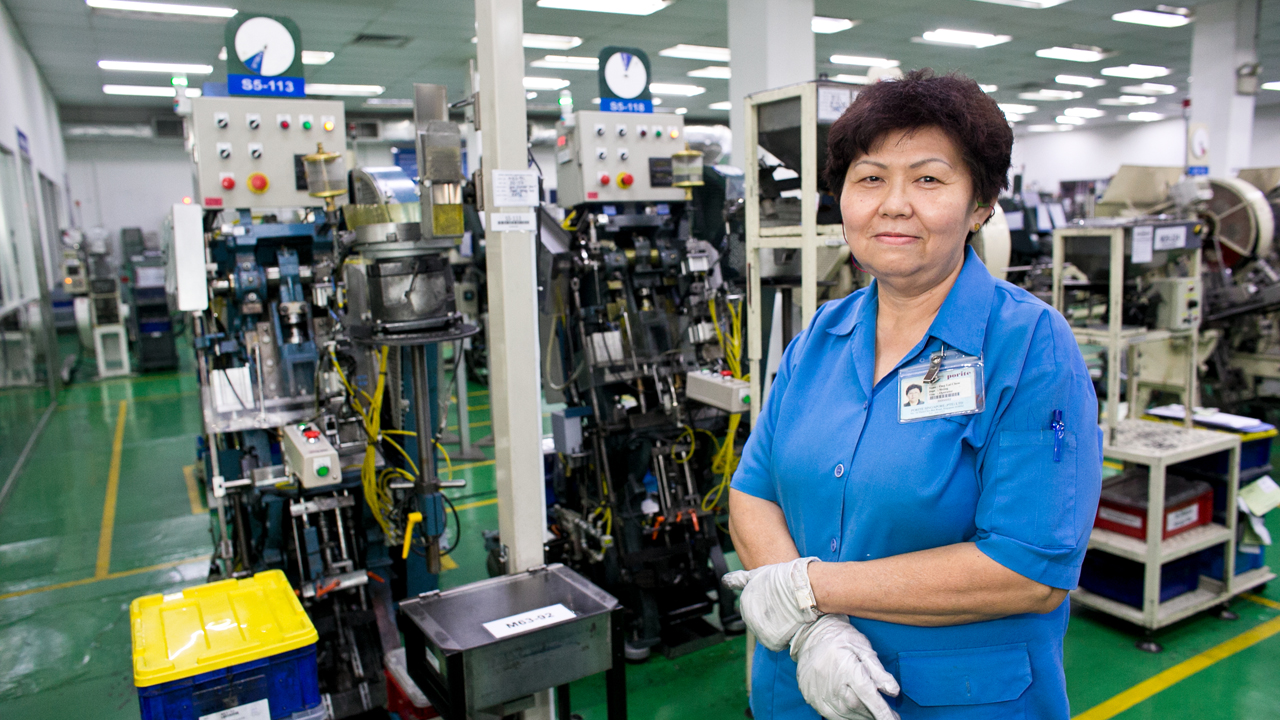
I was given a quick brief on the work processes and handed a set of uniform and production floor shoes to put on. Then it was off to the workstation.
The Current State
As an operator, I was tasked to pour ball bearings into a machine hopper for sizing. It sounded easy enough, but ended up being quite tedious.
The ball bearings were packed in plastic containers and could weigh anything between three to 13 kg. I know because I had to weigh each container before emptying it into the machine. And the machine hopper was taller than me!
I had to lift myself, on tip toes at times and stretching my arms to the maximum, to make sure the ball bearings ended up in the machine and not all over the floor.
The machine was also placed at a certain height, making it difficult for me to peer inside to make sure everything was going well.
When I reached my third container, my shoulders began to ache. This was something Madam Ong had experienced for the past few years.
“I spend money to buy massage oil and my husband will massage my shoulders and back for me when I go home every day,” she quipped.
That wasn’t all – during the sizing process, the machine can often stall, with the whole process having to be restarted several times.
The Job Re-design
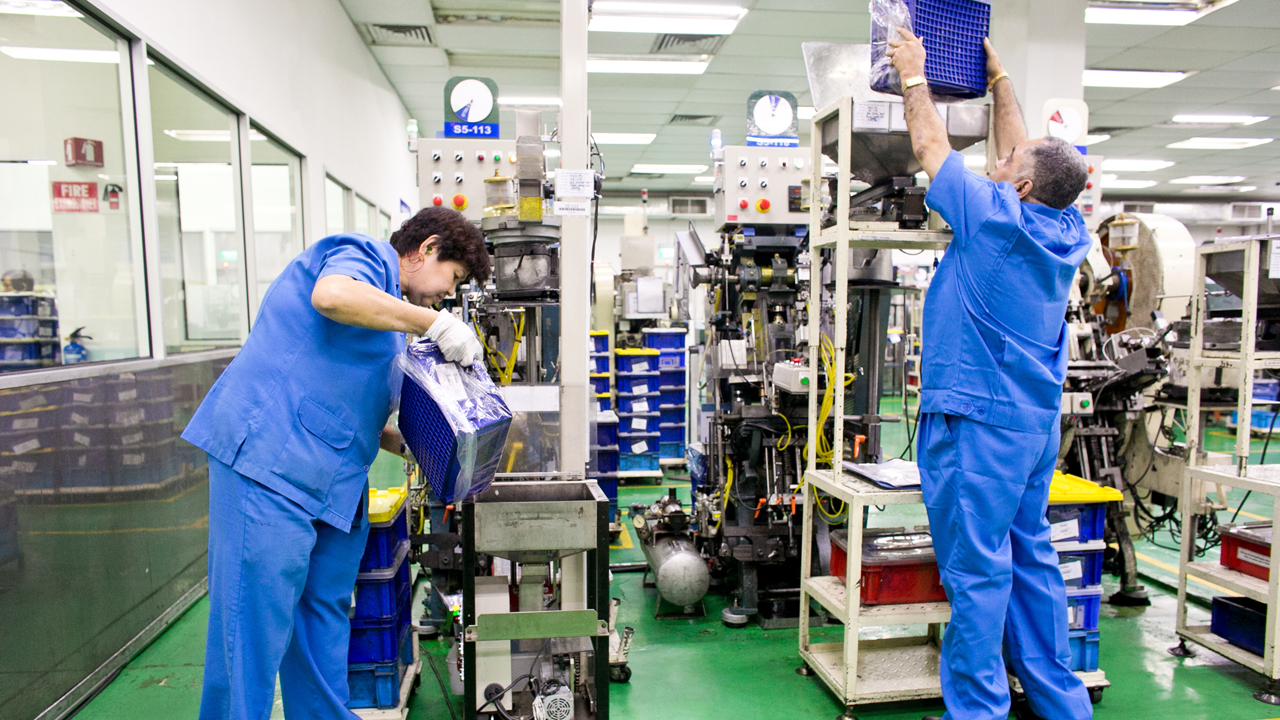
Mature workers like Madam Ong had been voicing out these issues to their management. The management listened, and did something to remedy the situation.
The company also realised that the process was not only affecting the health of the workers, it was also slowing down productivity.
It decided then to pilot a re-designed machine for the same work process, by bringing down the height of the machine hopper to waist level.
I tried out the re-designed machine, and to my relief, I did not have to raise my arms carrying the heavy container of ball bearings anymore.
I was also able to monitor the sizing process and swing into action faster when the machine stopped and had to be re-started. This saved a lot of production time.
The most important part – no more backaches and shoulder pain!
On top of raising productivity, the re-designed machine meant no more pain and a lot more gain for both the mature worker and the company. That, is definitely a step in the right direction.